Subsea Chemical Injection Systems
In the early 1990s, all chemicals supplied to subsea production systems were delivered through dedicated umbilical hoses, with individual dosage rates controlled from the host facilities. However, this required larger diameter and more costly umbilicals. One option was to deliver chemicals through a single hose and then to distribute them to the individual users on the seabed. However, this required reliable subsea chemical injection valves.
In 1993, a Joint Industry Project was established by Ferranti Subsea Systems Ltd. (now part of Aker Solutions) in order to test marinised versions of metering valves and to assess their suitability for subsea service. Valves tested included the company’s own products, plus a number of other valves provided by third party suppliers. The test programme concluded at the end of 1995 with two main findings. First, the existing valves were all prone to fouling and would benefit from redesign. Secondly, two different types of valve were recommended: one type for high flows and another for low flows. Today, all subsea chemical injection valves are designed to maximise turbulence through the restriction, thus reducing the likelihood of blockage. Also, for low flows, fixed orifices are typically recommended, whilst high flows utilise variable orifices.
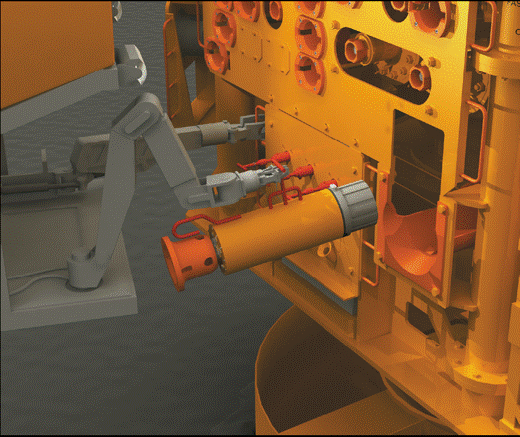
Remote injection valve replacement
(Image © Cameron)
Whilst subsea distributed chemical injection systems are now commonplace, fouling has continued to pose challenges. Recognising this, the umbilical suppliers launched the Blockage Avoidance in Subsea Injection and Control Systems (BASICS) project in 2007. This concluded in 2013 with the issue of two technical reports and a series of e-learning training modules.